Common Fault Analysis of Plate and Frame Filter Press
- Damage to the Plates
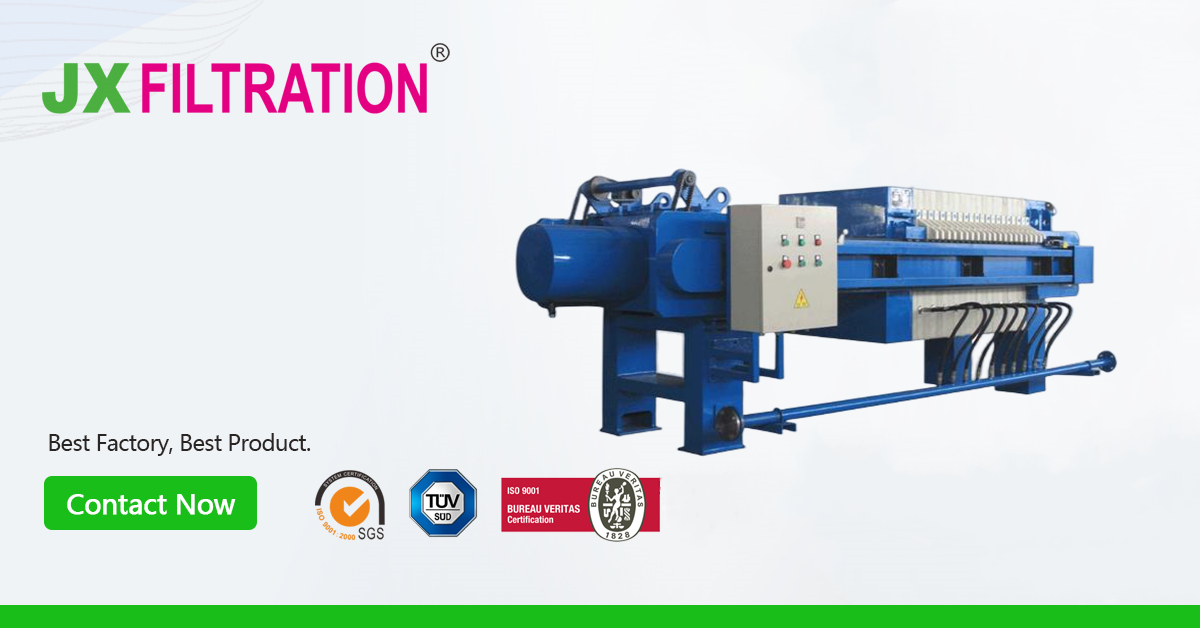
Causes of plate damage include:
-
When sludge is too thick or dry blocks remain, it can cause blockage at the feeding port. At this point, there is no medium between the filter plates, only the pressure from the hydraulic system itself. Prolonged pressure can easily lead to plate damage.
-
Insufficient feeding or inappropriate solid particles in the feed can also cause excessive force on the plate and frame, leading to damage.
-
If the outlet is blocked by solids, or the feeding valve or outlet valve is closed during startup, pressure has no way to escape, resulting in damage.
-
Improper cleaning of the filter plates can sometimes lead to medium leakage. Once leaked, the edges of the plate and frame will be washed out with small grooves, and the large amount of leaked medium makes it impossible for the pressure to rise, and the mud cake cannot form.
Methods to eliminate corresponding faults:
-
Use a nylon cleaning scraper to remove sludge from the feed port.
-
Complete this cycle to reduce the volume of the filter plate.
-
Check the filter cloth, clean the drainage port, check the outlet, open the corresponding valves, and release the pressure.
-
Carefully clean the filter plates and repair them.
- Leakage Between Plates and Frames
The main reasons for leakage between plates and frames are:
-
Low hydraulic pressure.
-
Wrinkles on the filter cloth or holes in the filter cloth.
-
Blockage on the sealing surface.
The treatment of leakage between plates and frames is relatively simple. It is sufficient to correspondingly increase the hydraulic pressure, replace the filter cloth, or use a nylon scraper to remove blockages on the sealing surface.
- Failure to Form Mud Cake or Uneven Mud Cake
There are many reasons for the failure to form or uneven mud cake. Insufficient or too thin feeding, or blockage phenomena, can cause such issues. To address these faults, the causes should be carefully investigated, the exact problem identified, and then targeted measures taken to solve the problem. The main solutions include increasing the feeding, adjusting the process, improving the feeding, cleaning or replacing the filter cloth, clearing blockages, cleaning the feeding hole, cleaning the drainage hole, cleaning or replacing the filter cloth, increasing pressure or pump power, low-pressure start, and continuously increasing pressure.
- Slow or Unstable Movement of Filter Plates
Sometimes, excessive oil or dirt on the guide rods can cause slow movement of the filter plates, and they may even deviate and fall off. In such cases, it is necessary to clean the guide rods in a timely manner, apply butter to ensure lubrication. It should be noted that it is strictly forbidden to apply thin oil to the guide rod, as thin oil can cause slippery conditions, and personnel operating or inspecting in this area may easily slip and cause personal injury accidents.
- Hydraulic System Faults
The hydraulic system of the plate and frame filter press mainly provides pressure. When oil is injected into oil chamber A, the piston moves to the left, compressing the filter plate to make it airtight. When oil is injected into oil chamber B, the piston moves to the right, releasing the filter plate. Due to precision manufacturing, hydraulic system failures are rare, and regular maintenance is usually sufficient. Nevertheless, due to wear, oil leakage may occur approximately every year. In such cases, the O-ring seal needs to be repaired and replaced. Common hydraulic faults include inability to maintain pressure and inappropriate advancement of the hydraulic cylinder. The main reasons for the inability to maintain pressure include oil leakage, wear of O-rings, and abnormal operation of the solenoid valve. Common remedies include removing and inspecting valves, replacing O-rings, cleaning and inspecting solenoid valves, or replacing solenoid valves. Inappropriate advancement of the hydraulic cylinder is apparently caused by trapped air inside. In such cases, the system should be bled, which can usually be quickly resolved.
- Poor Adhesion Between Mud Cake and Filter Cloth
Methods:
- Check whether the flowability or concentration of the filtrate has changed. If abnormal flowability or concentration is observed, extend the filtration time, reduce the moisture content of the mud cake, and achieve good detachment of the mud cake from the filter cloth.
- Check whether the dosage of additives is appropriate and adjust it.
- Check whether the capacity and pressure of the feed pump are appropriate. If not, take measures such as changing the filtration time.
- If the filter cloth is adhered to, causing the mud cake to not be removed properly, tie the bottom end of the filter cloth on both sides of the filter plate or compression plate together. This allows the filter cloth and filter plate to be pulled together, facilitating the smooth removal of the mud cake.
- Insufficient or Empty Filter Chamber
Insufficient filling of the filter chamber or formation of an empty chamber can lead to imbalances in pressure on both sides of the filter plate, and excessive pressure difference on both sides can cause damage to the filter plate. The most common cause of this fault is blockage in the channels. The internal sludge channels and diaphragm pump sludge pipelines inside the plate and frame should be checked. Common blockages include small pieces of broken cloth or folded filter cloth blocking the channels, or the sludge being too viscous, and the pipeline not being backwashed during filtration, causing blockage in the pipeline.
- Folding of Filter Cloth
(1) Check whether the flowability or concentration of the filtrate has changed. If abnormal flowability or concentration is observed, extend the filtration time, reduce the moisture content of the mud cake, and achieve good detachment of the mud cake from the filter cloth.
(2) Check whether the dosage of additives is appropriate and adjust it.
(3) Check whether the capacity and pressure of the feed pump are appropriate. If not, take measures such as changing the filtration time.
(4) If the filter cloth is adhered to, causing the mud cake to not be removed properly, tie the bottom end of the filter cloth on both sides of the filter plate or compression plate together. This allows the filter cloth and filter plate to be pulled together, facilitating the smooth removal of the mud cake.
- Turbid Filtrate
If the filter cloth is damaged, mud infiltrates from the rupture and is discharged as it is, making the filtrate turbid. Filtration cannot proceed at this point. Check the filter cloth at the source of the turbid liquid and repair or replace the damaged filter cloth.
- Repair of Filter Plates
The repair technique for filter plates is as follows:
After several years of use, the filter plates may develop some grooves at the corners due to certain reasons. Once grooves appear, they can quickly enlarge, eventually affecting the formation of the mud cake. Initially, the mud cake becomes soft, then turns into a semi-fluid state, and finally, the mud cake cannot be formed. Due to the special material of the filter plates, they are difficult to repair and can only be replaced with new ones, resulting in high spare parts consumption. During this period, we tried some repair agents, but the effect was not good. Recently, when using oil-based repair agents, the situation finally improved, and the trial effect was very good, achieving a good sealing effect.
Specific repair methods are as follows:
-
Clean the grooves to expose fresh surfaces, and use small saw blades or similar tools for cleaning.
-
Mix black and white repair agents in a 1:1 ratio.
-
Apply the mixed repair agent to the grooves, filling them slightly higher.
-
Quickly cover the filter cloth, squeeze the filter plates together, so that the repair agent adheres to the filter cloth, and at the same time, squeeze the grooves flat.
-
After squeezing for some time, the adhesive naturally takes shape and no longer changes. At this point, it can be used normally.
Any Requirements, Contact Us Now!
Kris
Email/Teams: kris@filtrationchina.com
Mobile/Whatsapp/Wechat: +86 18980776200
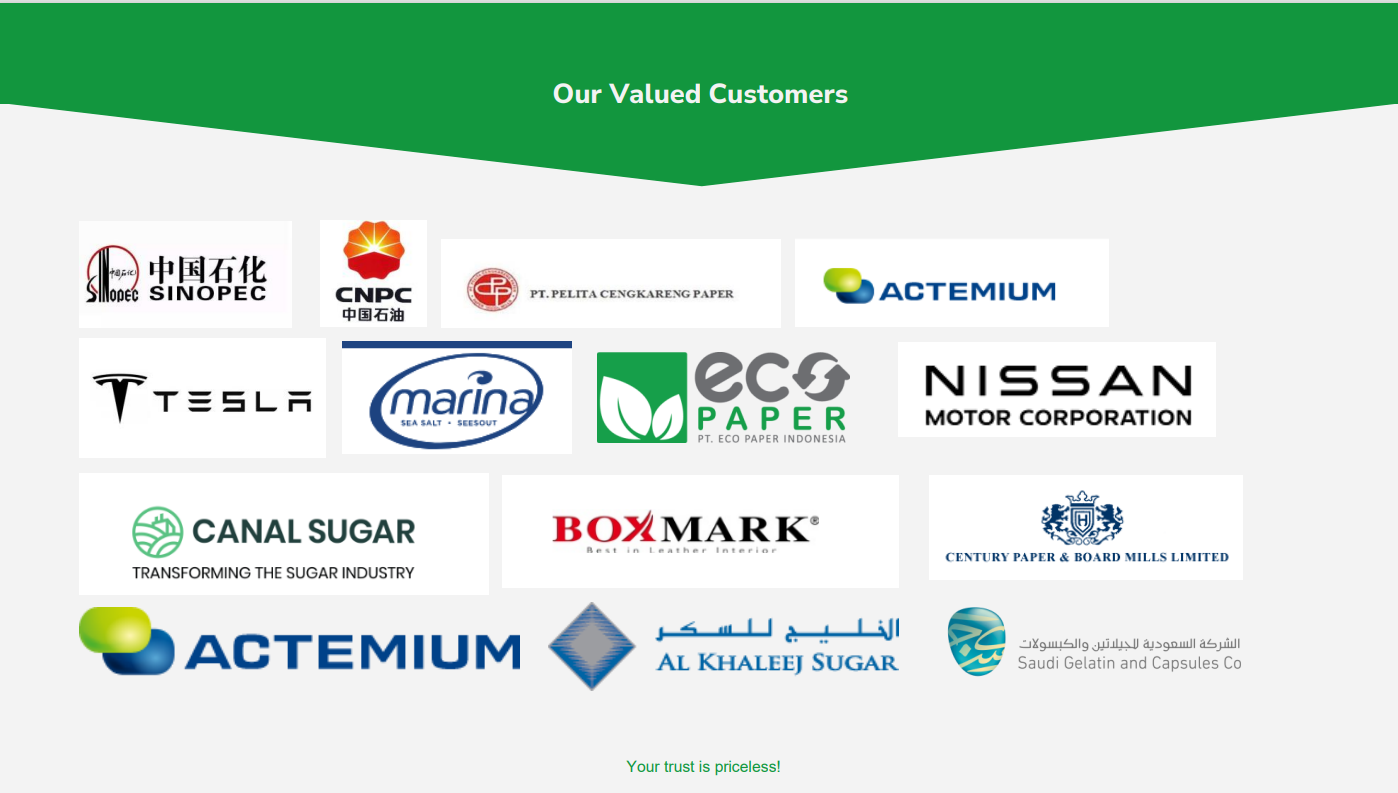