Plate and Frame Filter Press
Filter Plate Repair
After several years of use, filter plates may develop grooves at the corners for various reasons. Once these grooves appear, they can quickly expand, eventually affecting the formation of the filter cake. Initially, the filter cake becomes soft, then turns semi-slurry, and eventually, the filter cake cannot form. Due to the special material of the filter plate, it is difficult to repair, and replacement is often required, resulting in high spare parts consumption. We have experimented with various repair agents, and the recent use of oil-based repair agents has shown promising results, achieving effective sealing.
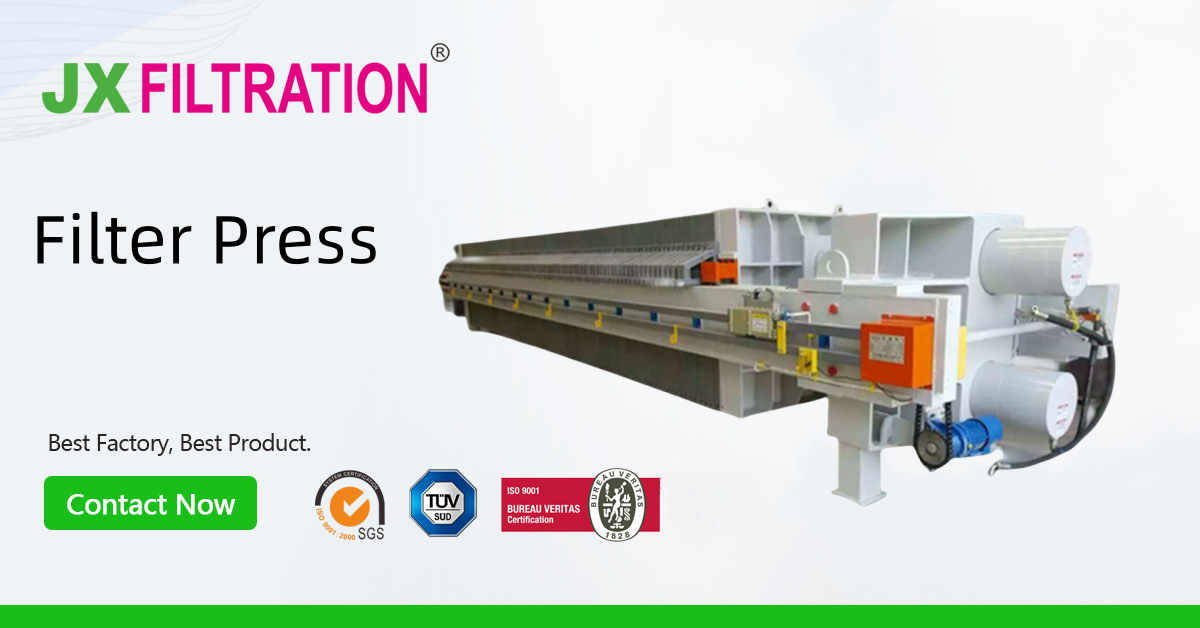
Specific repair steps are as follows:
-
Clean the grooves, exposing fresh surfaces, which can be done using small saw blades or similar tools.
-
Mix black and white repair agents in a 1:1 ratio.
-
Apply the mixed repair agent to the grooves, ensuring even coverage.
-
Quickly cover with filter cloth, press the filter plates together to bond the repair agent and filter cloth, simultaneously smoothing the grooves.
-
After pressing for some time, the adhesive will solidify, and the repair will be complete. At this point, the filter can be used as usual.
Safety Operating Precautions for Plate and Frame Filter Press
-
While the filter press is in operation, do not insert feet, hands, or head into the space between filter plates or observe the belt conveyor or central trough from the open gaps between the plates. Avoid placing tools on the hooks or handles of the filter plates.
-
Do not operate switches when there are people on the frame, top of the machine, or main beam.
-
The hydraulic part of the filter press must have an installed electrical contact pressure gauge.
-
Avoid wearing high-heeled shoes or working barefoot. Do not insert the head or hands between filter plates during the unloading process.
-
Do not operate buttons with gloves. Use a wooden shovel (bamboo pieces) for unloading.
-
Check the flexibility and reliability of operation buttons before work. During unloading, synchronize the discharge mechanism.
-
Before operation, check for foreign objects between the filter plates and any wrinkles in the filter cloth. Clean promptly if found.
-
During the filtration process, observe the filtered liquid. If damage is detected, note the plate number and promptly repair or replace the filter cloth.
-
Check for any deformation or breakage of the filter plates. Replace them promptly. When replacing filter plates, remove the filtrate nozzle first.
-
Rinse the filter cloth according to regulations to increase its permeability and improve filtration efficiency.
-
Before stopping, stop feeding first, unload all materials in the filter press, and then stop. It is strictly forbidden to stop with material in the press.
-
After the filter cake is discharged, clean the residual waste in each filter plate with a plastic shovel promptly.
-
When cleaning the filter frames and filter cloth after unloading, ensure that the channels are unobstructed, and no residue adheres to the sealing surface or the feeding channel.
-
When installing filter plates, handle them evenly to prevent collisions, impacts, or uneven forces that could damage the handles or sealing surfaces.
-
Replace damaged filter cloth promptly. When installing the filter cloth, ensure it is flat without folding to prevent damage or leakage during plate and frame compression.
-
Store disassembled filter plates neatly to prevent warping or deformation.
-
Ensure the sealing surface of the filter plate is clean and wrinkle-free. The filter plates should be arranged vertically and neatly on the main beam, avoiding any uneven placement, as this could prevent proper compression.
-
During the process of discharging filter cake, it is strictly forbidden to insert the head or limbs between the filter plates.
-
Promptly replace leaky water and damaged filter cloths, wash and air-dry them, and store them neatly for unified processing.
-
Maintain a smooth and wrinkle-free surface on the filter cloth. Handle filter plate handles gently, ensuring that the plates are compressed evenly and do not deviate from the compression centerline.
Any Requirements, Contact Us Now!
Kris
Email/Teams: kris@filtrationchina.com
Mobile/Whatsapp/Wechat: +86 18980776200
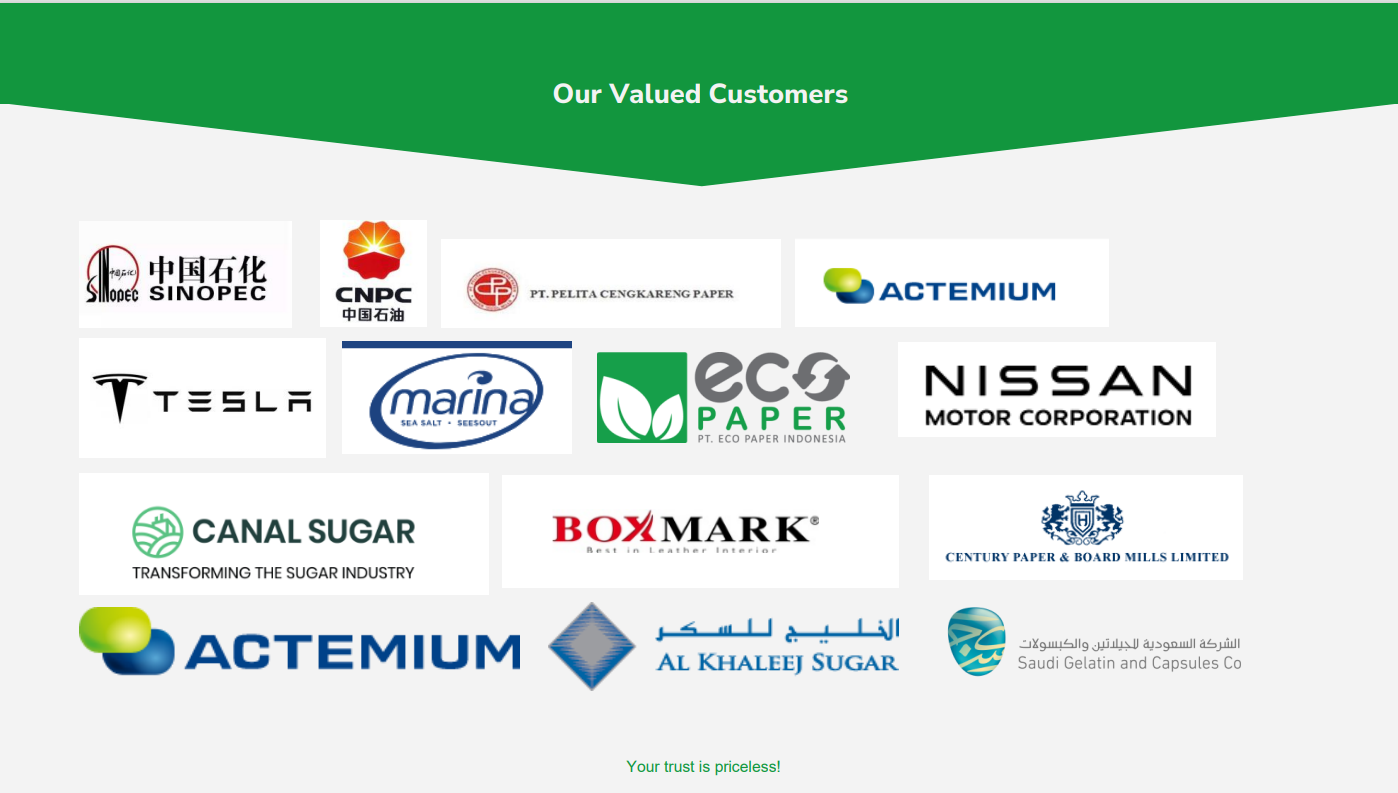