Common Problems Of Filter Press
Q1: What should I do if there is wear and groove on the edge of the filter plate?
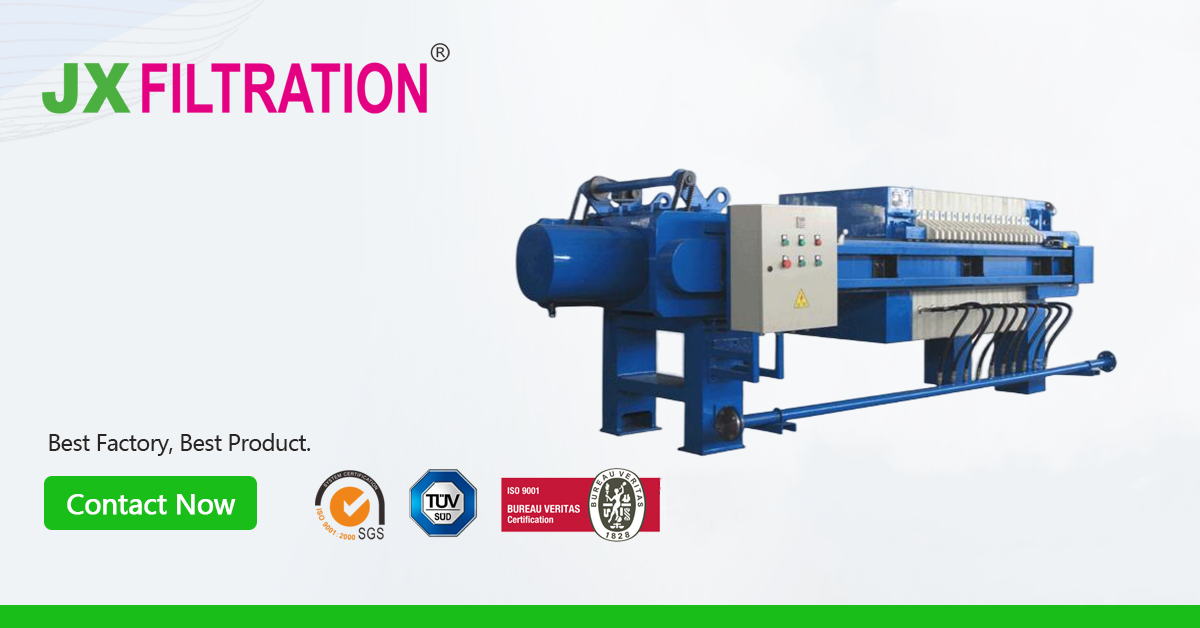
A1: After a period of use, the edge of the filter plate may develop grooves due to the impact of particulate matter and other factors. If these minor damages are not taken seriously, it can easily lead to improper formation of the filter cake, resulting in the enlargement of the grooves and difficulty in forming the filter cake.
Generally, the first step is to clean the debris in the groove of the filter plate to make it smooth and tidy. Then, according to the instructions for use of the repair agent, apply the repair agent evenly on the groove of the filter plate. Finally, prepare the leather strip, put it on, and press it to quickly bond the two together.
It is worth mentioning that during the bonding process, it is necessary to ensure the smoothness of the groove. The firm bonding of the filter plate and the leather strip completes the repair of the filter plate.
Q2: What are the reasons for spraying material between the filter plates?
A2: Reason 1: It is caused by excessive feed pressure. Many users do not install pressure gauges on the feed pipeline, resulting in uncontrolled feed pressure, which ultimately leads to material spraying.
Reason 2: The top pressing force for tightening the filter plates is insufficient. After the feed pressure increases, the force between the filter plates will push them apart, causing material spraying.
Reason 3: There are impurities attached to the sealing surface of the filter plate, such as filter cake. After the filter cake is removed, the sealing surface should be cleaned.
Reason 4: The sealing surface of the filter plate has through grooves or the filter plate itself is damaged.
Q3: How to solve the problem of water leakage and material running between the filter plates?
A3: Generally, there are four main reasons for this situation:
It may be caused by excessive feed pressure, resulting in high filtration rate; or low hydraulic pressure of the hydraulic system; there are wrinkles in the filter cloth or voids on the filter cloth or blockage on the sealing surface; lastly, the filter cloth is not cleaned according to the regulations, or the cleaning effect is not good enough to meet the requirements.
When this fault occurs, first increase the corresponding clamping pressure. If there are problems with the filter cloth or sealing surface, replace the filter cloth in time, clean the impurities on the sealing surface, and clean the filter cloth on time. Finally, reduce the feed pressure to the normal value.
Q4: What causes the low movement speed of the filter plate? How to solve it?
A4: The guide rods are easily contaminated by oil stains, which will reduce the movement speed of the filter plate and even cause the filter plate to not move along the track, deviating and falling off.
When the phenomenon of slow movement occurs, the stains on the guide rod should be cleaned and kept clean, and lubricant should be evenly applied to its surface to ensure smooth movement of the guide rod.
Q5: How to operate if the filter plate cannot be opened?
A5: After the filter press is blown, the filter plate often fails to open or stops intermittently during loosening operation.
At this time, it is necessary to ensure that the filter plate is loosened and the pressure is vented to meet the pressure standard requirements. If the pressure is not completely vented, it will cause problems in the opening action of the filter plate due to the operation lock.
In addition, if the system operates for a long time and the loss is too great, and the hydraulic oil is not replenished in time, the insufficient oil supply will cause poor continuity of the hydraulic cylinder operation, resulting in intermittent phenomena.
Any Requirements, Contact Us Now!
Kris
Email/Teams: kris@filtrationchina.com
Mobile/Whatsapp/Wechat: +86 18980776200
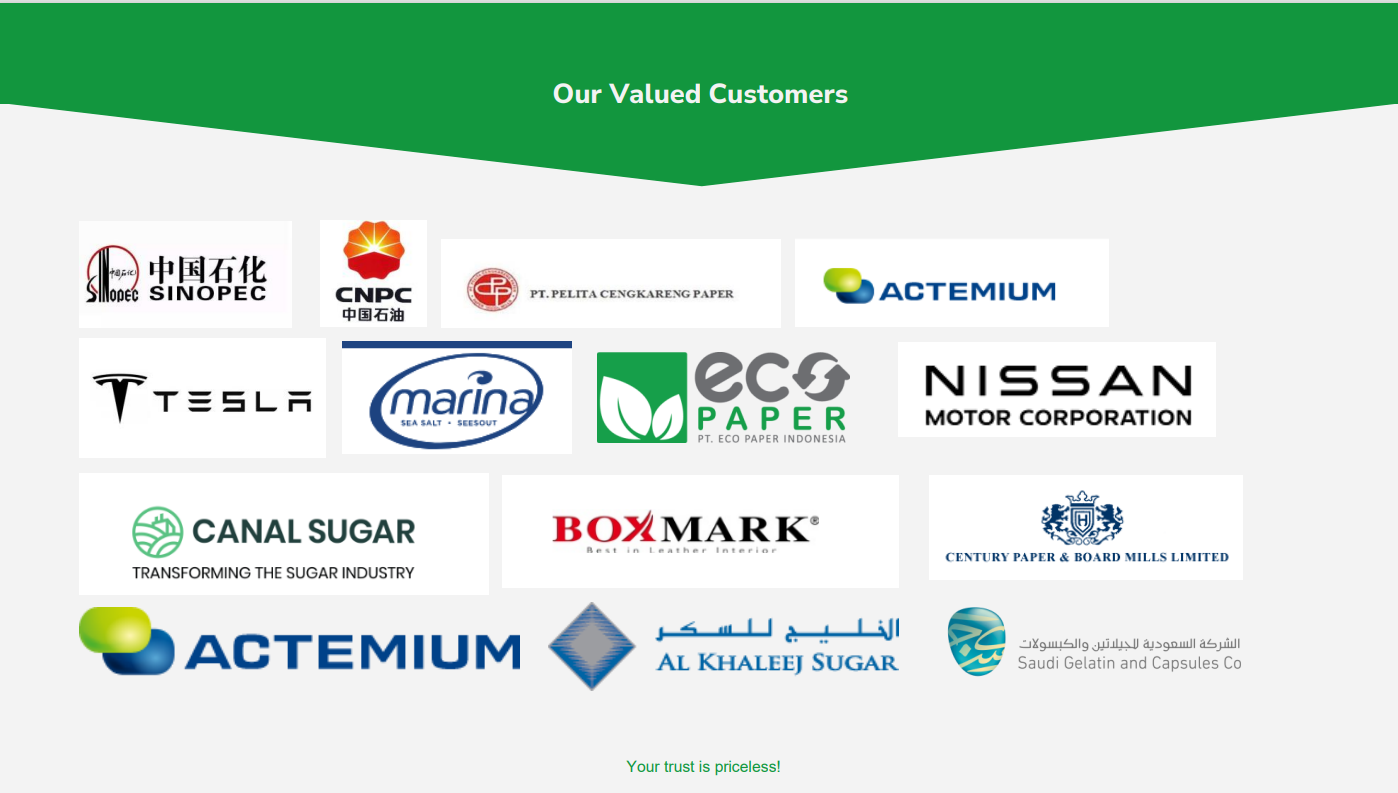