How to Choose Vibrating Sieve Screen
- Clarify Your Requirements:
Screening Purpose: Determine whether you need fine or coarse screening. For fine screening, such as high-precision grading of powders and fine particles, options like rotary vibrating screens or ultrasonic vibrating screens are suitable. For coarse screening, where quick separation of larger particles is required, linear vibrating screens, mining vibrating screens, or direct discharge screens are more appropriate.
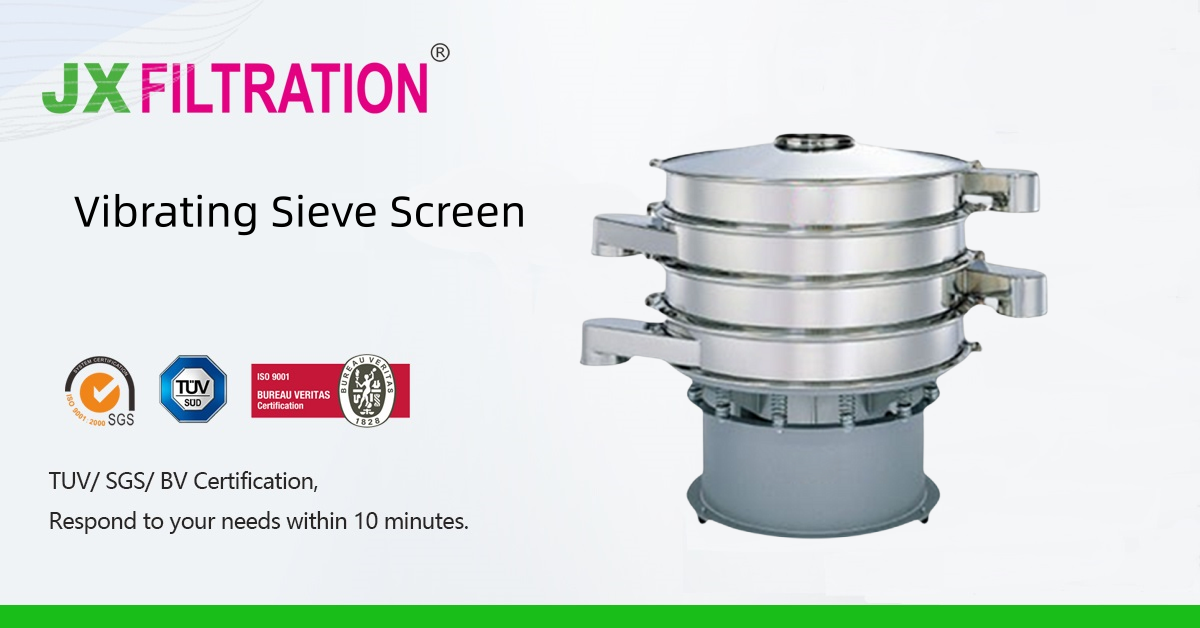
Processing Capacity: Estimate the processing capacity required based on production scale and output needs. Different models of vibrating screens have varying capacities, so ensure that the chosen equipment can meet the material handling needs of your production line.
Particle Size Distribution: Understand the particle size range and composition to select the appropriate mesh size and number of screen layers. For materials with a wide range of particle sizes, a double-layer or multi-layer screen might be needed.
Moisture Content: If the material has high moisture content, it may adhere to the screen, affecting screening efficiency. In this case, select a vibrating screen with anti-clogging and anti-blocking features or opt for screens with a larger inclination angle and dynamic design.
Material Shape: Different material shapes (e.g., flakes, spheres, cylinders) affect flowability during screening. The difficulty of screening and the requirements for the vibrating screen vary based on the shape of the material.
Corrosiveness: For materials that are corrosive, choose vibrating screens made from corrosion-resistant materials, such as stainless steel.
- Evaluate the Performance Parameters of the Vibrating Screen:
Screen Surface Size: The screen surface size directly affects screening efficiency and capacity. Generally, the screen width should be at least 2.5 to 3 times the largest particle size to avoid clogging.
Mesh Size: Select the appropriate mesh size according to the material’s particle size to be screened. Mesh size should comply with industry standards and production requirements, which vary depending on the type of vibrating screen.
Vibration Frequency and Amplitude: Vibration frequency and amplitude are key factors influencing screening efficiency. Higher vibration frequency and appropriate amplitude can enhance screening efficiency, but excessive values may damage the equipment or generate too much noise.
Motor Power: The motor power determines the driving force and energy consumption of the vibrating screen. Underpowered motors may not meet the operational requirements, while overpowered motors will increase energy costs and equipment expenses. Select the motor power based on the screen model and processing capacity.
- Consider the Quality and Structure of the Equipment:
Material: The material used in the construction of the vibrating screen impacts its wear resistance, corrosion resistance, and service life. High-quality vibrating screens generally use high-strength steel or stainless steel for critical components like the screen frame and mesh.
Welding Process: Check whether the welding points on the vibrating screen are firm and smooth. The quality of the welding affects the overall strength and stability of the equipment.
Structural Design: A well-designed structure can improve the efficiency and stability of the vibrating screen. For example, the screen box should have sufficient strength and rigidity to withstand the impact and vibration of the material, and the selection and arrangement of damping springs should effectively reduce equipment vibration and noise.
Any Requirements, Contact Us Now!
Kris
Email/Teams: kris@filtrationchina.com
Mobile/Whatsapp/Wechat: +86 18980776200
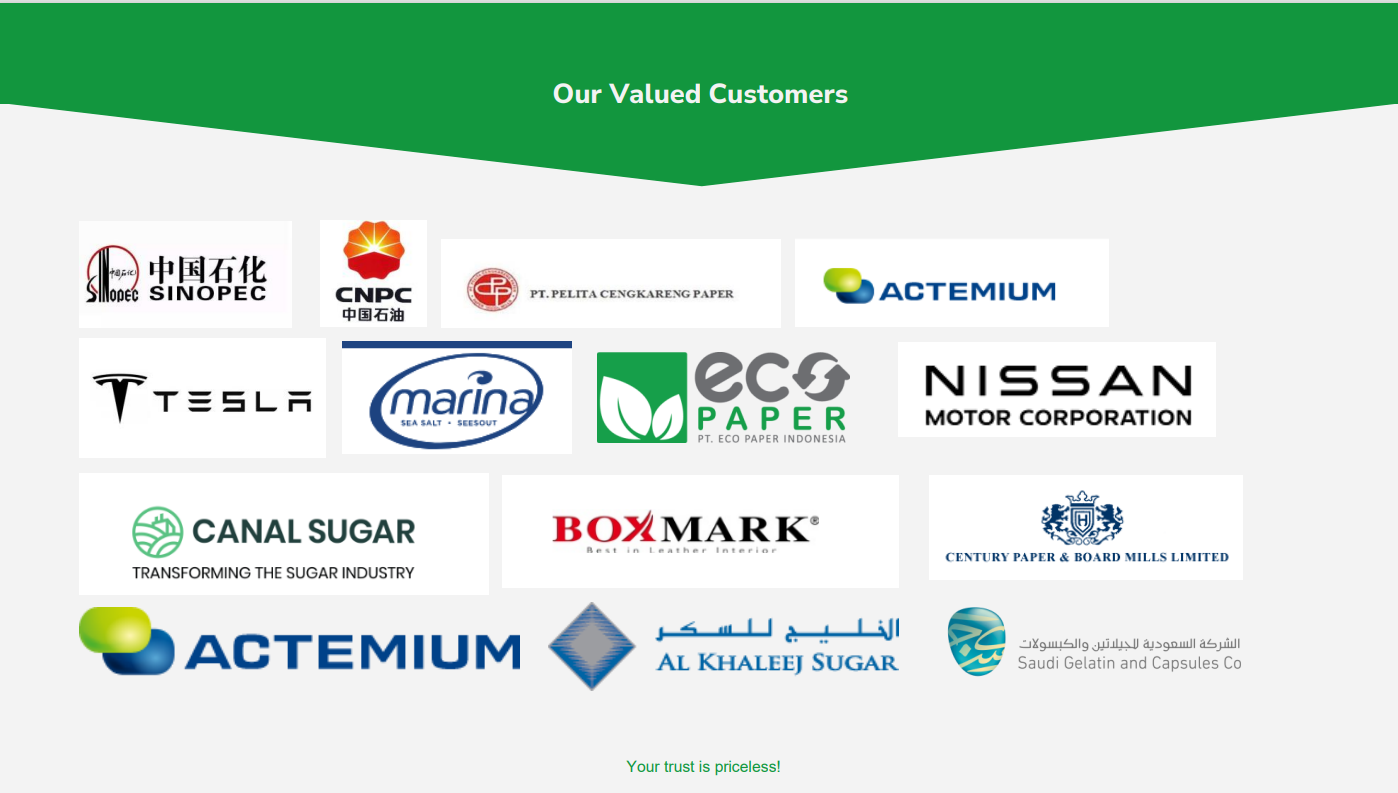